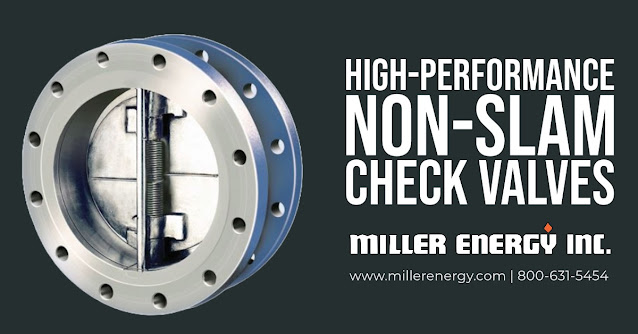
The industrial sector demands reliable and efficient machinery to support complex processes.
High performance non-slam check valves are integral to these industrial systems, ensuring smooth, uninterrupted operations.
Advantages of using non-slam check valves in industrial process applications:
Swift Response Time: Non-slam check valves react quickly to flow changes. They have a short disc stroke, which means the valve disc travels a small distance from fully open to fully closed. This quick response time prevents the sudden surge or water hammer, thus protecting the pipeline systems.
Minimized Water Hammer: Water hammer occurs when fluid in motion suddenly stops or changes direction. It creates a shock wave in the pipeline, damaging pipes, joints, and other equipment. The design of non-slam check valves enables them to close quickly but gradually before reverse flow begins. This mechanism minimizes the possibility of water hammer, enhancing the lifespan and operational efficiency of the system.
Reduced Pressure Drop: Non-slam check valves have a streamlined flow path and low head loss design, allowing optimal flow with minimal resistance. This reduced pressure drop translates to more energy-efficient operations and, in turn, reduces operational costs.
Longer Equipment Lifespan: Non-slam check valves are constructed from robust and high-quality materials, ensuring a longer service life than traditional check valves. They are resistant to corrosion, erosion, and wear, which reduces the frequency of replacements and maintenance, saving time and resources in the long run.
Low Maintenance: The design of non-slam check valves, with its anti-slam feature, minimizes wear and tear on valve components. This low-maintenance aspect of the non-slam check valves means fewer operational disruptions and reduced maintenance costs.
Versatility: Non-slam check valves are suitable for various industrial applications, including chemical processing, power generation, water treatment, oil and gas processing, and more. Their adaptability across multiple industries makes them a cost-effective and reliable choice for managing process flow.
Compact Design: Non-slam check valves are often more compact than traditional check valves, making them ideal for installations where space is at a premium. The smaller footprint allows for more flexibility in system design and ease of installation.
Enhanced Process Efficiency: The quick response time, minimized water hammer, and reduced pressure drop of non-slam check valves collectively lead to a more efficient process operation. These factors ensure the smooth flow of process materials, minimize downtime and reduce operational costs.
High performance non-slam check valves are crucial in industrial process applications. Their numerous benefits, including swift response time, minimized water hammer, reduced pressure drop, and enhanced process efficiency, make them invaluable in maintaining smooth and cost-effective industrial operations.
Miller Energy, Inc.
https://millerenergy.com
800-631-5454